How core filling affects intumescent paint coatings
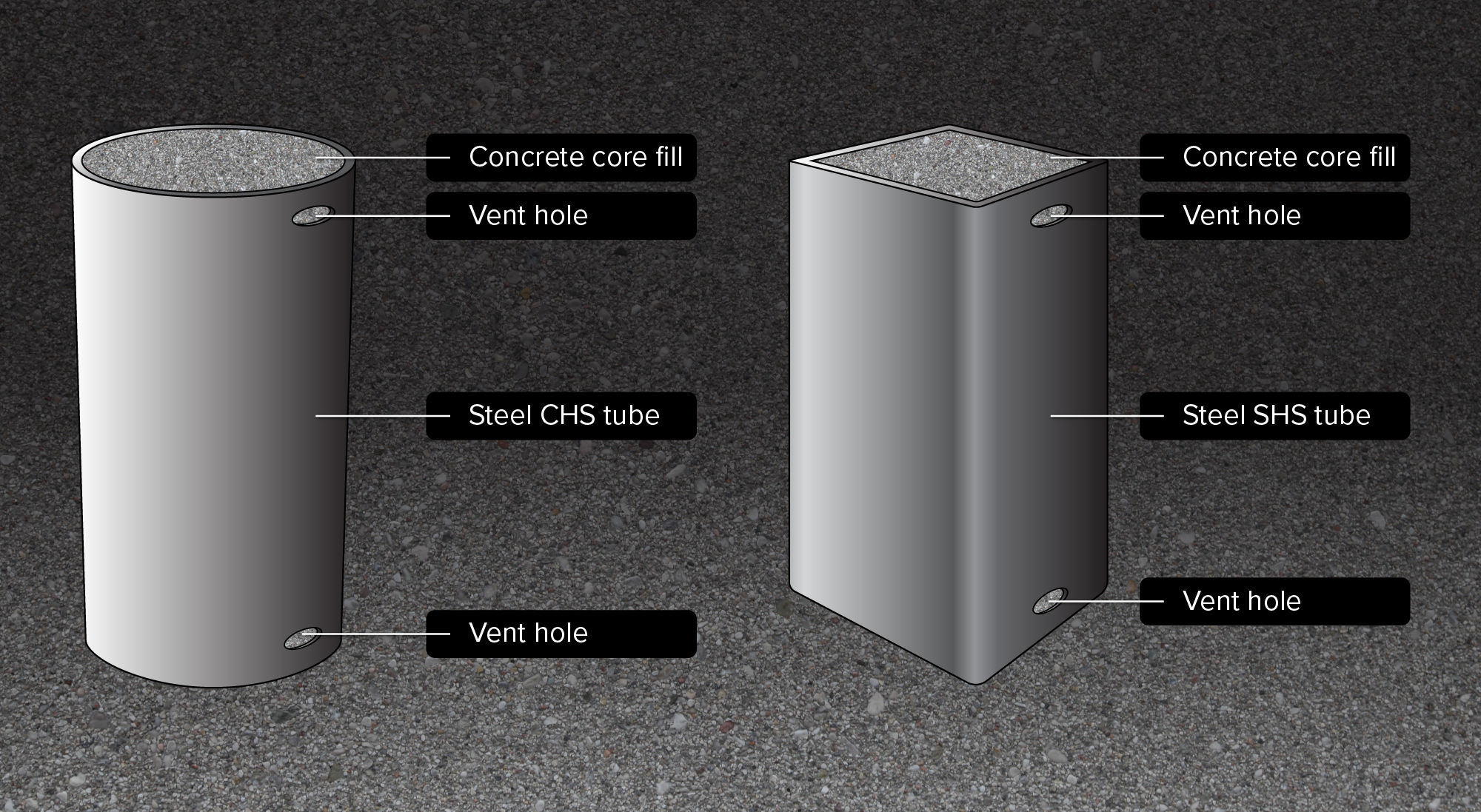
It provides additional options between:
- Upgrading the steel size
- Lowering DFTs
A grout or standard concrete mix (<40MPa) loosely packed concrete is adequate.
Mix lowers the Hp/A of the steel member and justifies a significant reduction in required dry film thickness of intumescent paint coatings to meet high FRLs.
The benefits of core-filling hollow section steel are:
- It lowers the Hp/A value
- The mix adds thermal resistance to the structural steel
- It forms a composite column with higher compressive capacity
- Lower film builds can have aesthetic advantages in terms of level of finish
learn more on the steelconstruction.info website (UK)
Download the PDF
click hereMore articles...
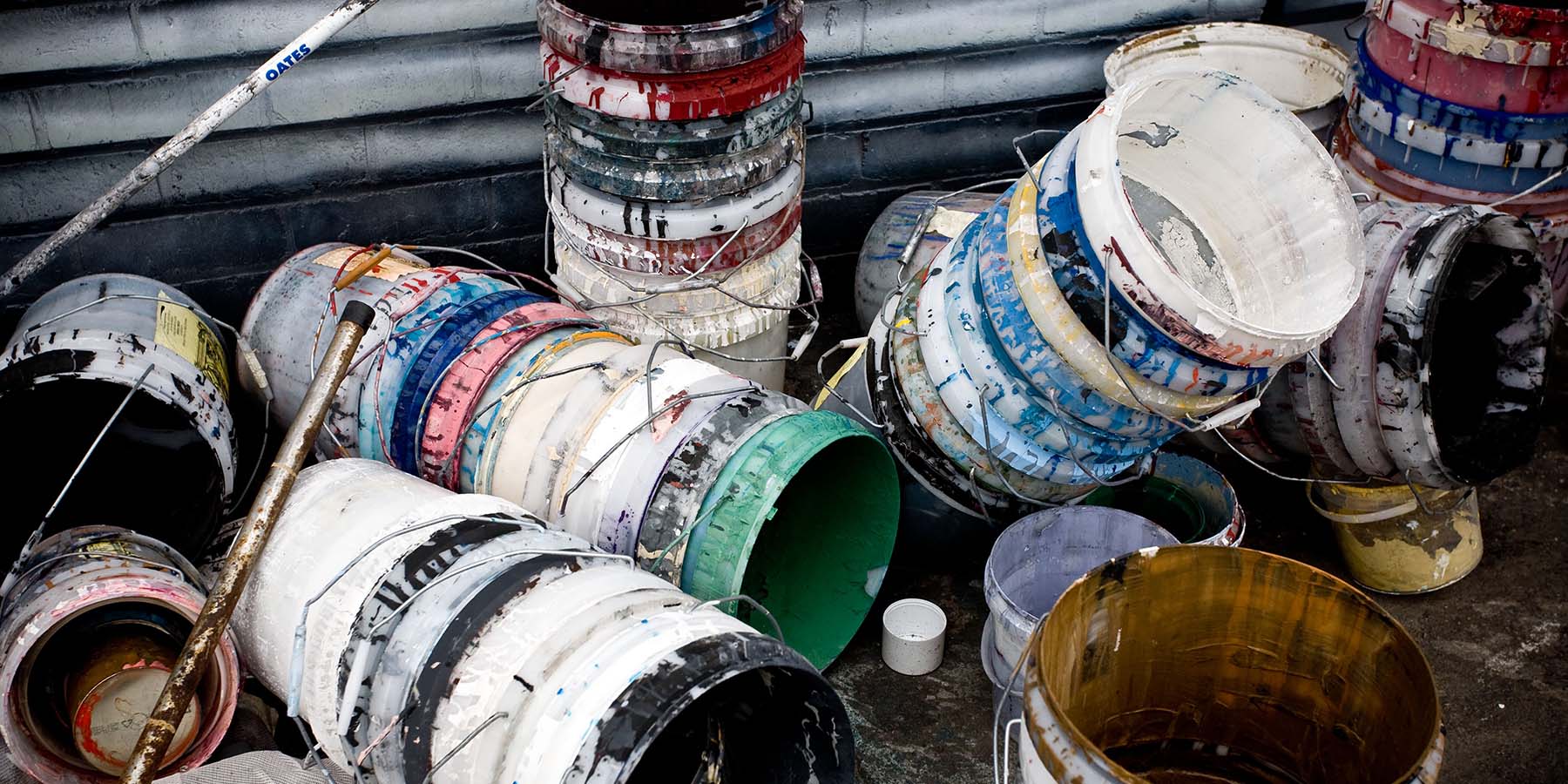
Intumescent coating types
There are a variety of intumescent coating types with different properties and application methods. Which type is the best for your situation?
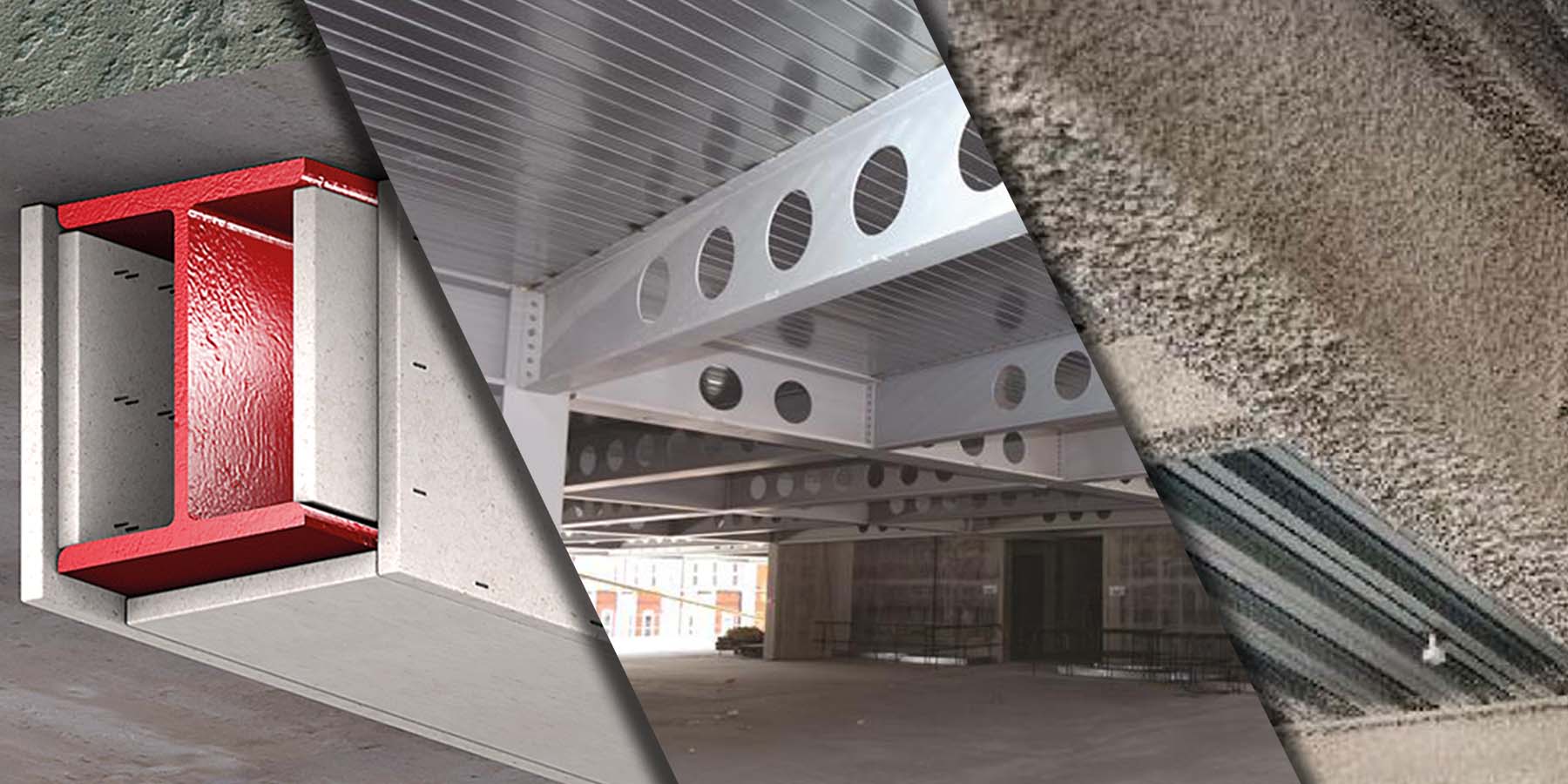
Passive fire protection methods
There are several ways to protect building structural work. Whilst some methods may be more prevalent, there is no one "best way" to protect a building's structure. The best method will most likely be determined by a number of factors, but here are your options.
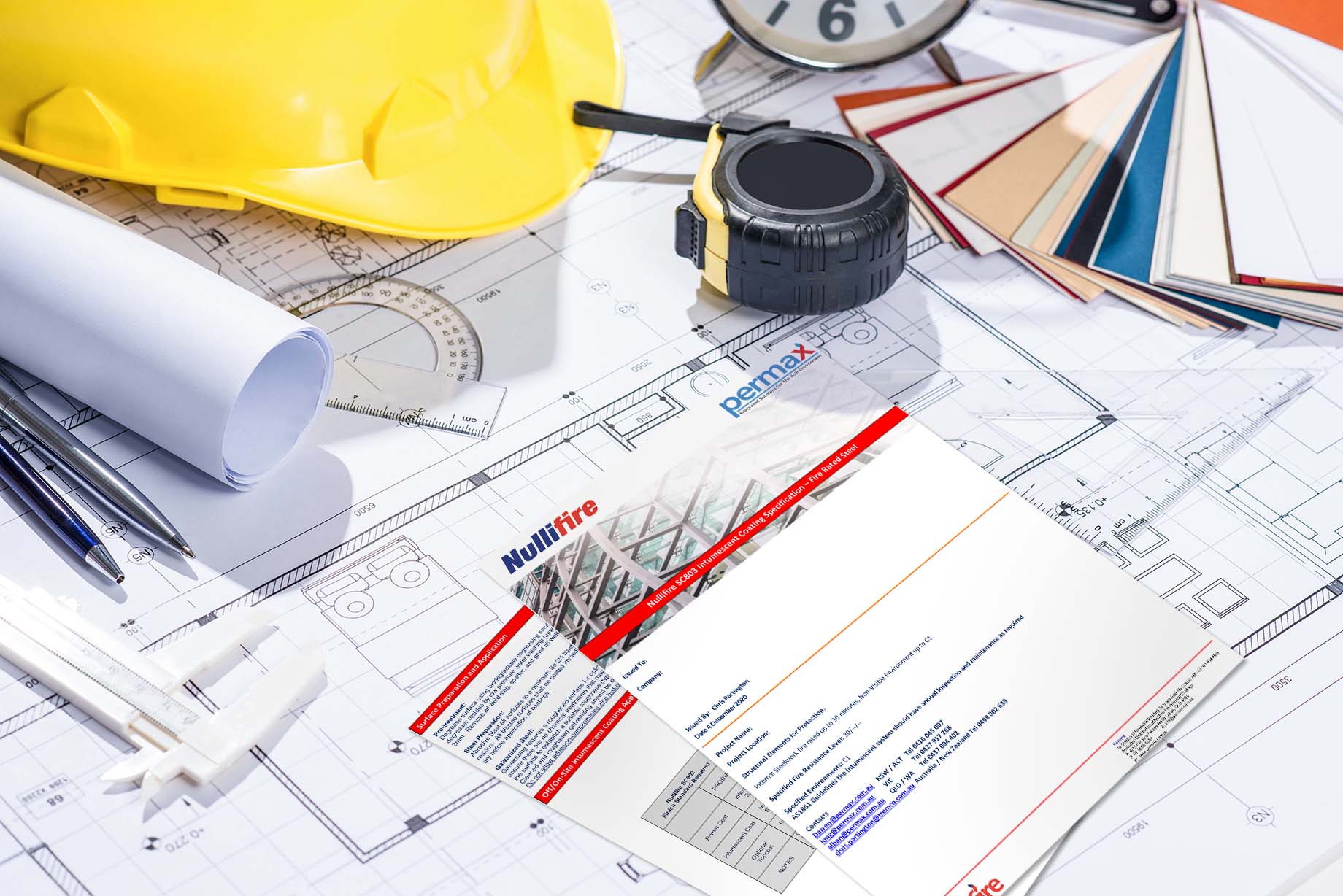
Intumescent paint coating specification templates
Access a range of templates supplied by manufacturers for the purposes of specifying their intumescent paint coating products for various FRLs and corrosivity ratings.
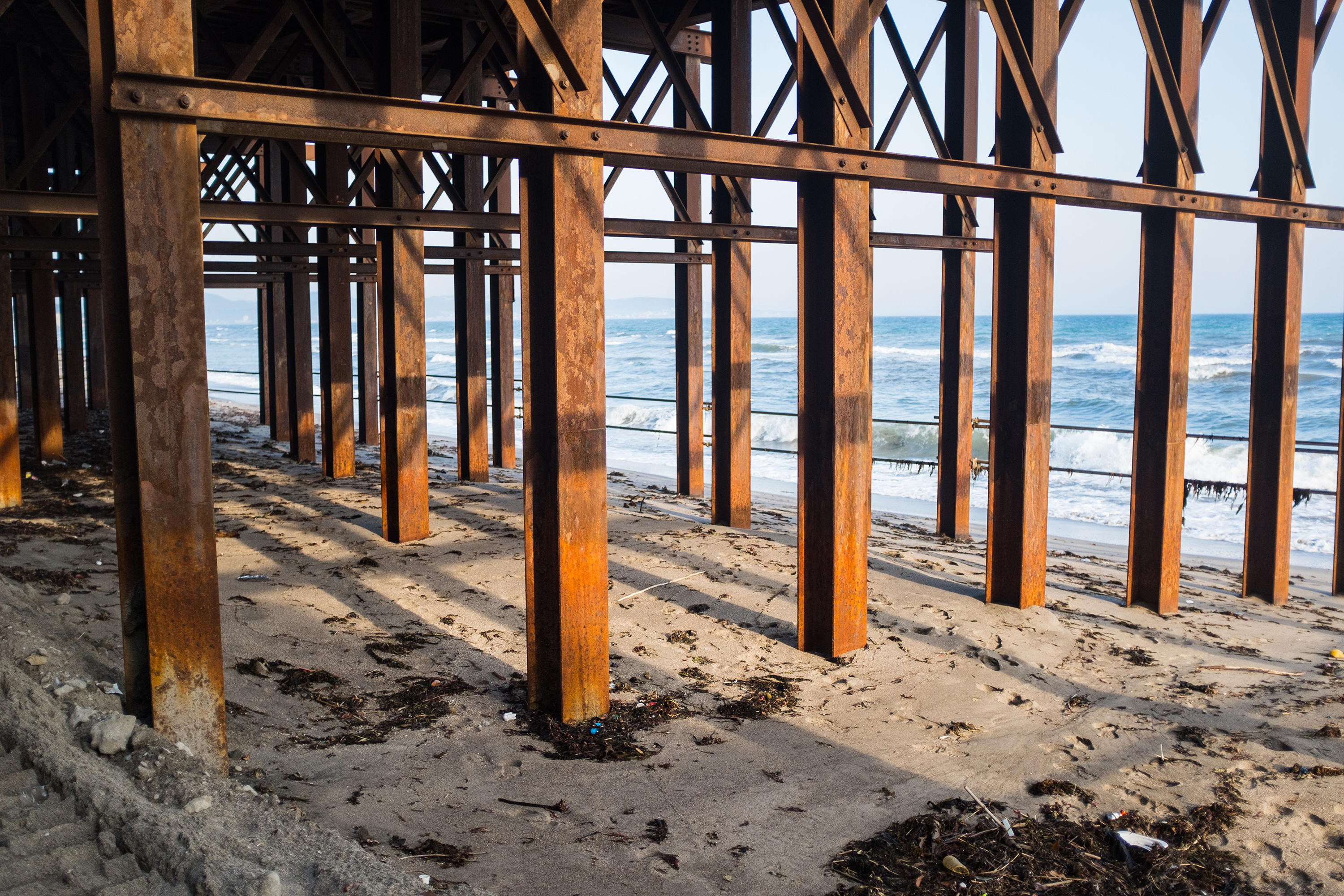
Intumescent paint coating corrosivity ratings in the Australian atmosphere
It's common knowledge that corrosion rates are affected by environmental factors, but do you know the various corrosivity ratings and their definitions?
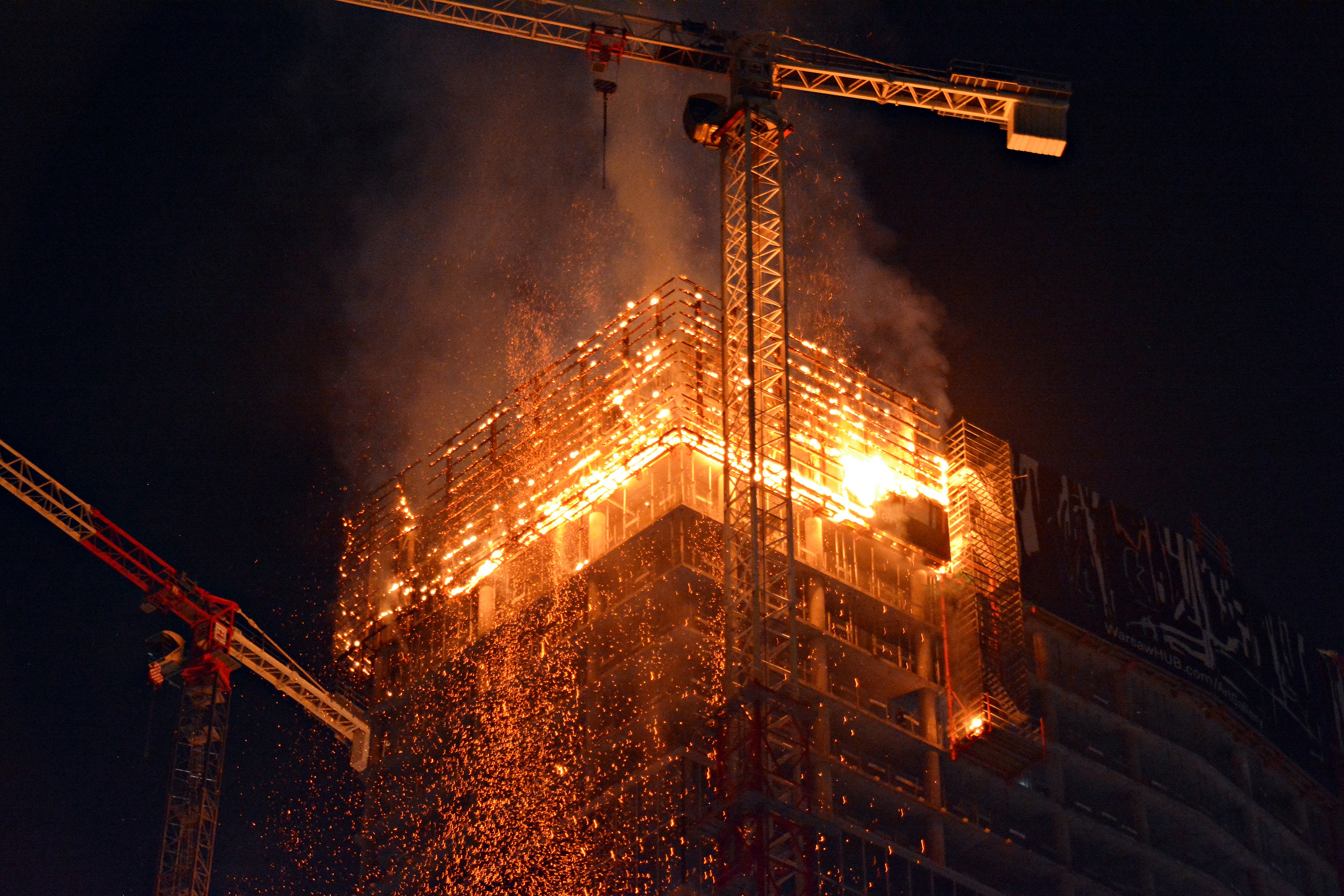
Limiting steel temperatures to maintain structural integrity
Maintaining structural adequacy on load-bearing steel is critical to the fire safety of building occupants, fire fighters and the surrounding built environment. Here's how limiting steel temperatures to maintain structural integrity relates to intumescent paint coatings.
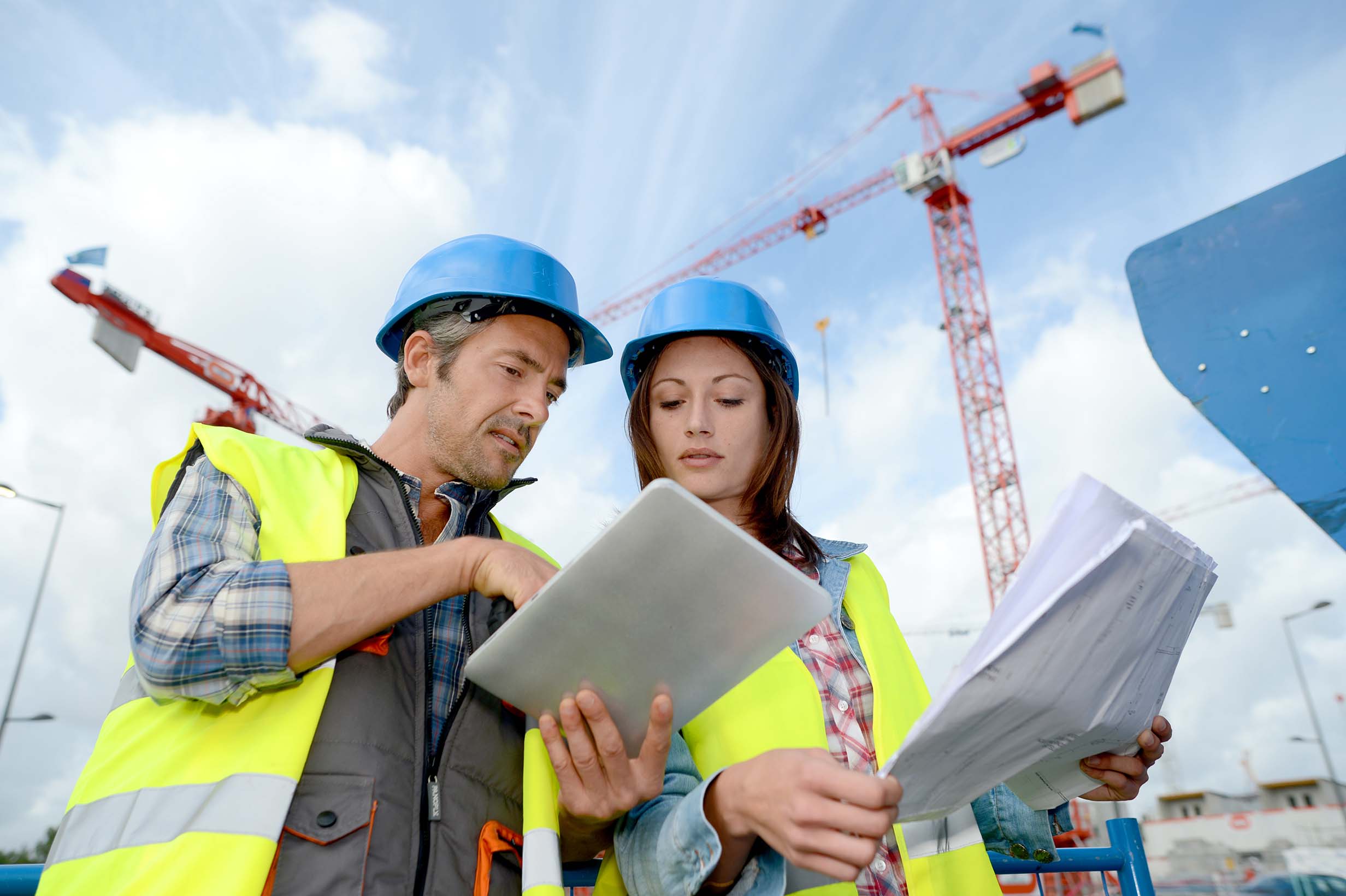
Getting help with intumescent paint coatings
The specifying and application of an intumescent coating system is a highly specialised task that requires considerable training and experience to accomplish correctly.
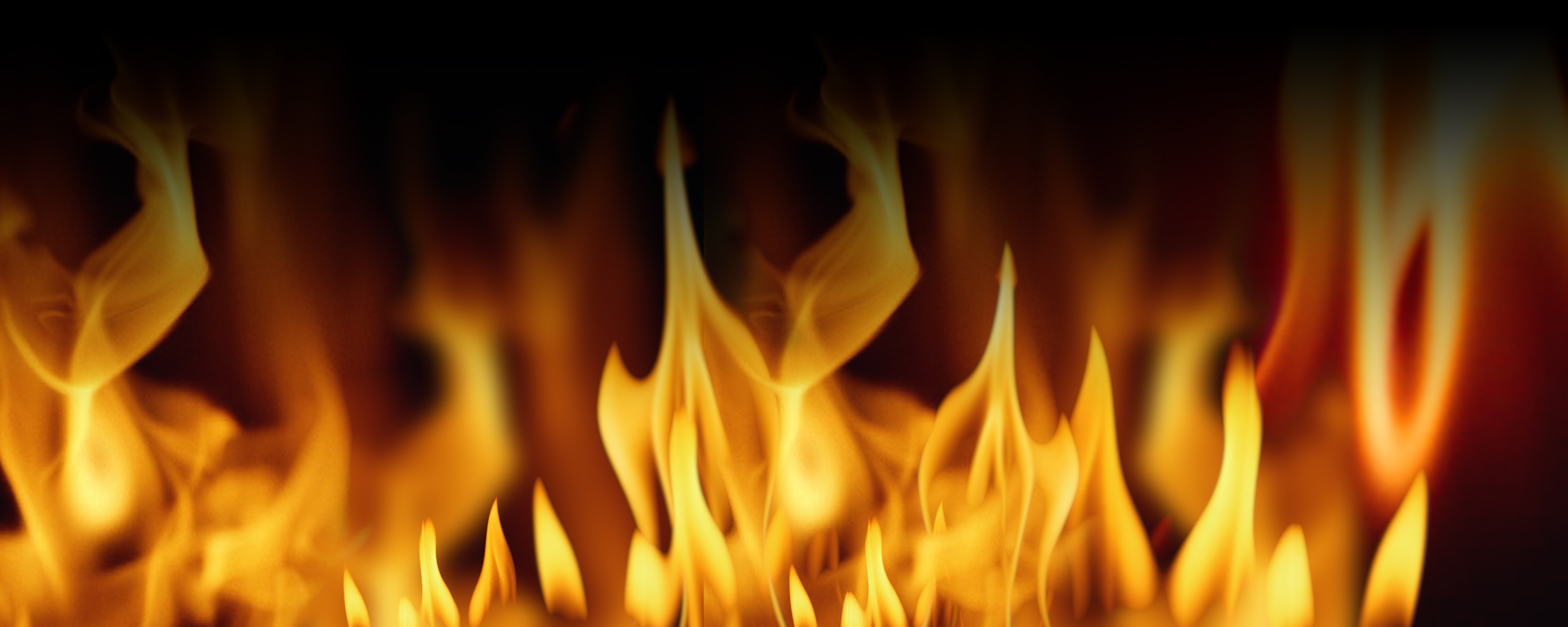
Fire types and severity
Different combustible materials burn at different temperatures which will have a bearing on the FRL of a given intumescent paint coating. This needs to be taken into account when specifying intumescent products so that the required FRL is ensured for the combustible materials that are likely to be encountered in a particular situation.
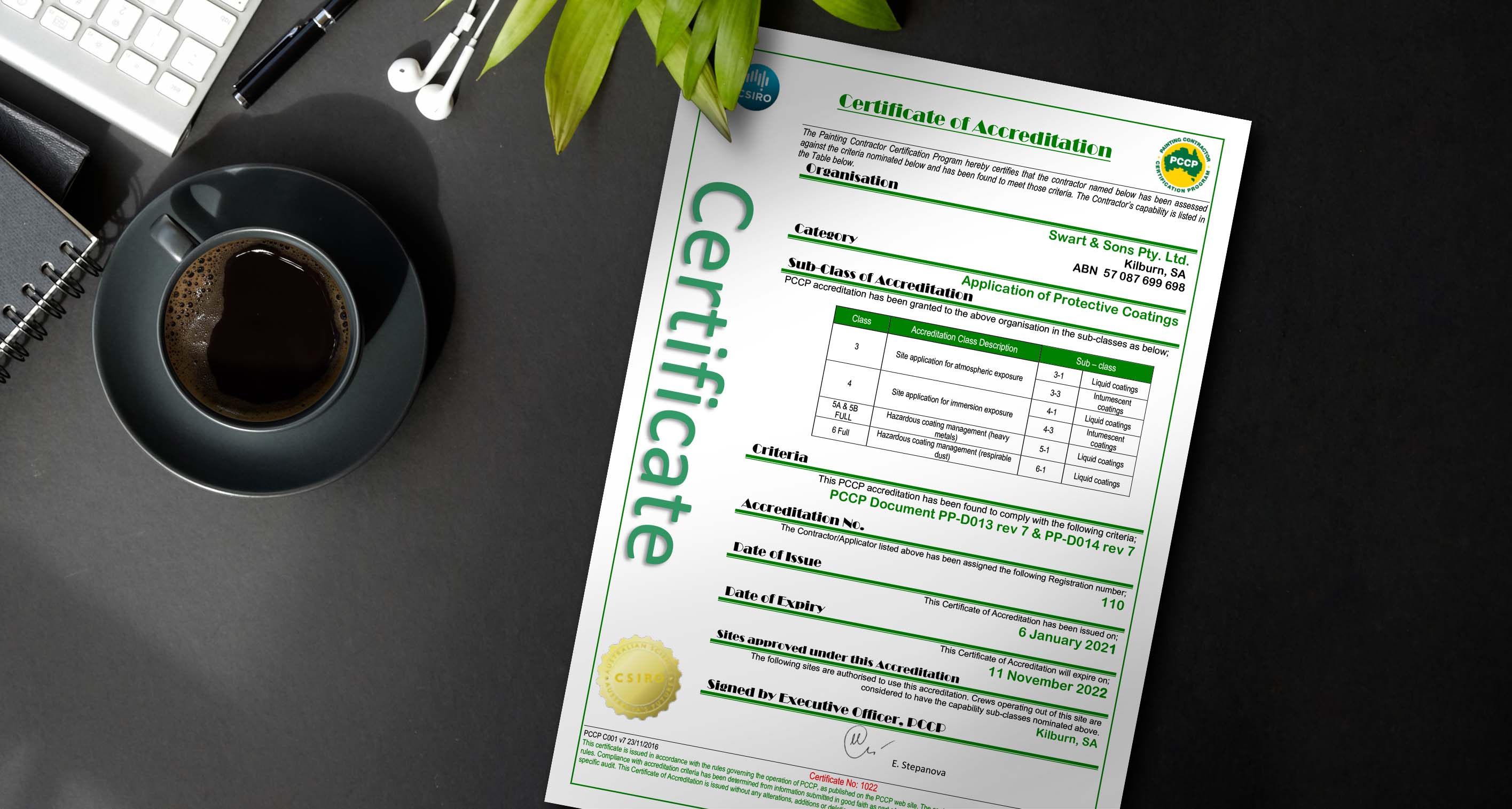
Quality assurance for intumescent paint coatings
We believe Painting Contractor Certification Program (PCCP) accreditation is paramount for passive fire protection contractors engaged in applying intumescent paint coating systems.
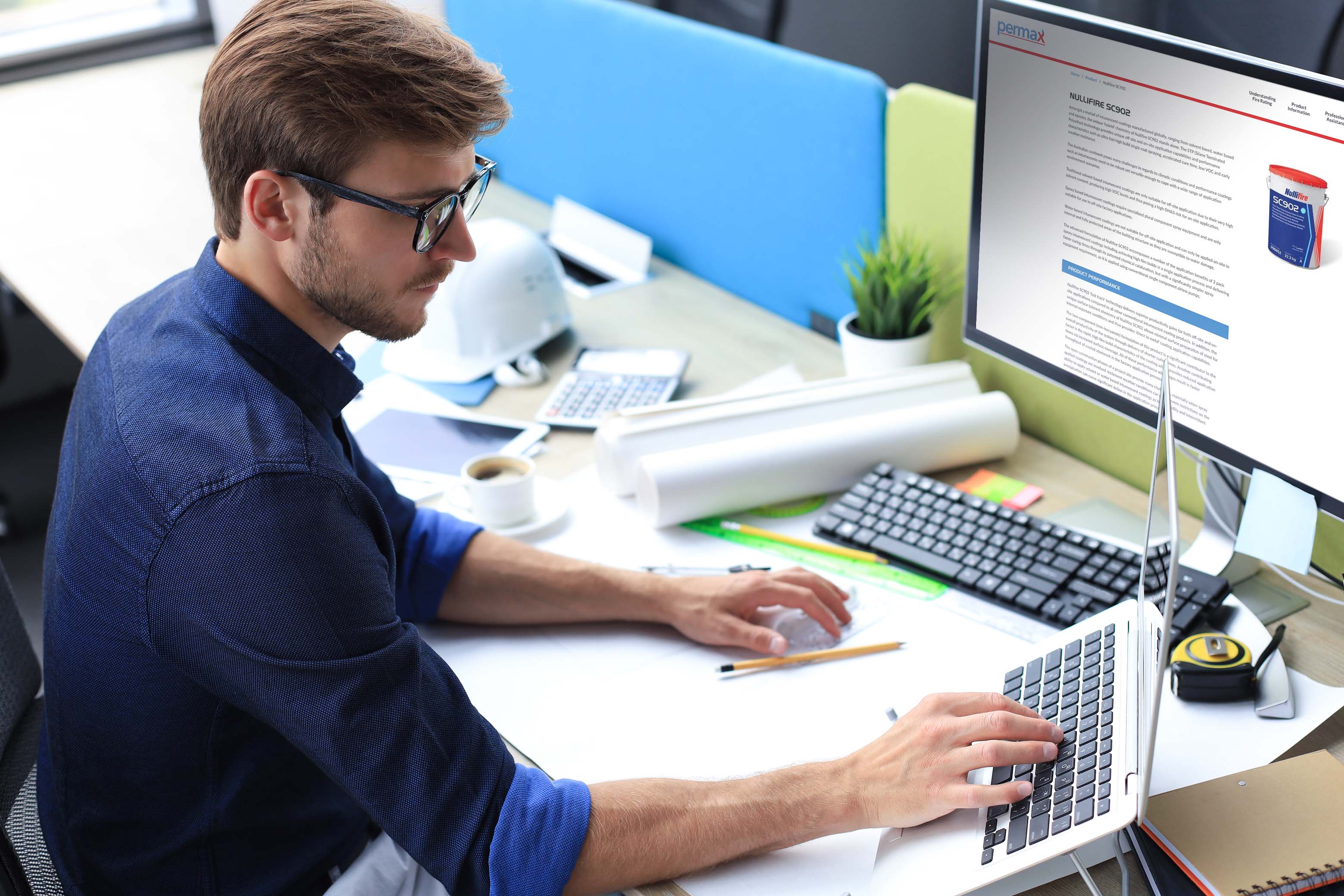
Specifying intumescent paint coatings
Whilst intumescent coating products may look just like paint, they have an important function (i.e. passive fire protection) that makes their specification a much more involved process.
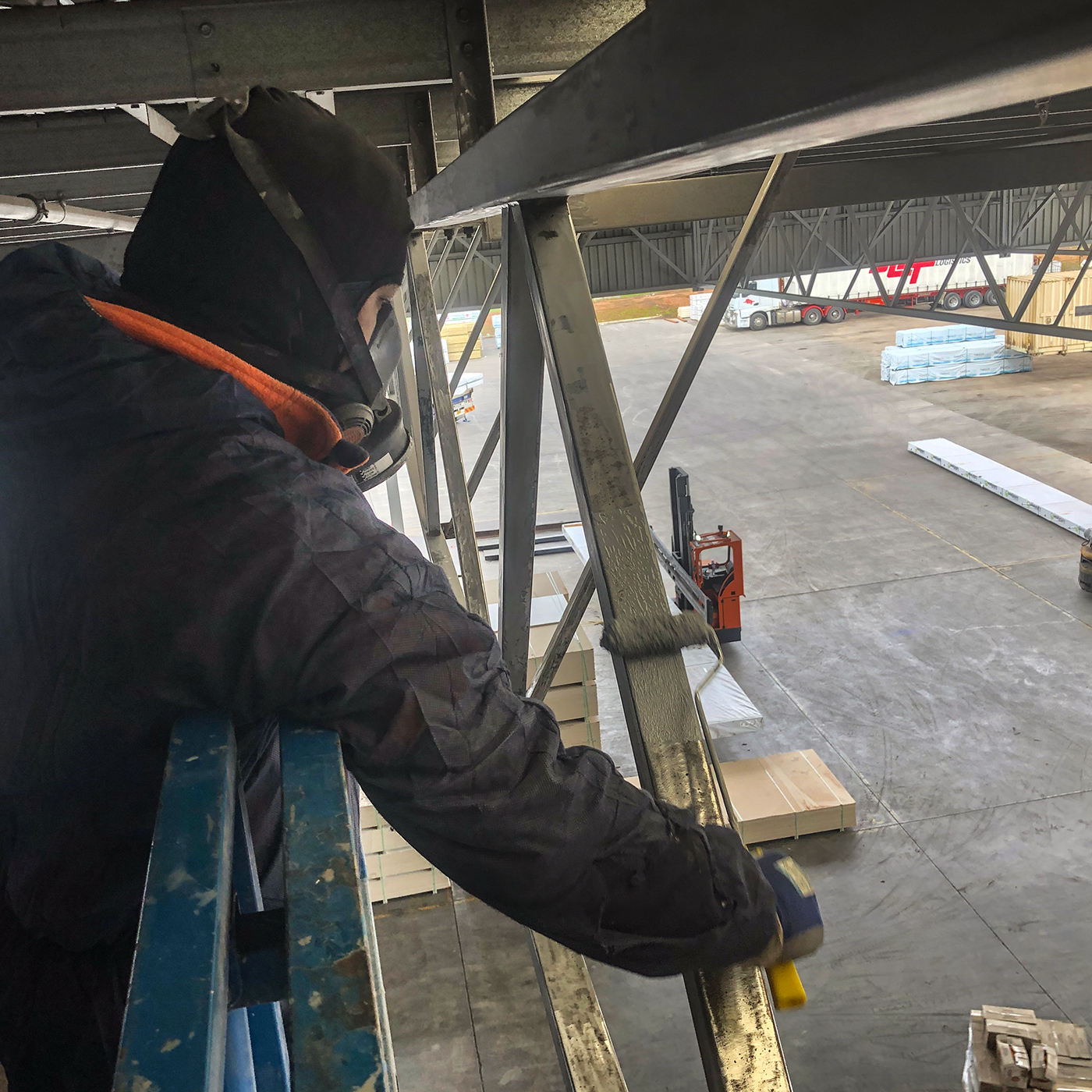
Applying intumescent paint coatings
Builders need to choose appropriately qualified subcontractors that are licensed to do work in the relevant state or territory, i.e. they are licensed to apply intumescent paint coatings.